The Science Behind Porosity: A Comprehensive Guide for Welders and Fabricators
Recognizing the elaborate devices behind porosity in welding is vital for welders and producers pursuing impeccable craftsmanship. As metalworkers dive into the midsts of this sensation, they reveal a world regulated by numerous elements that affect the development of these minuscule spaces within welds. From the make-up of the base materials to the details of the welding process itself, a wide range of variables conspire to either worsen or alleviate the existence of porosity. In this detailed overview, we will certainly unravel the science behind porosity, exploring its impacts on weld high quality and introduction progressed techniques for its control. Join us on this journey via the microcosm of welding flaws, where precision meets understanding in the quest of flawless welds.
Understanding Porosity in Welding
FIRST SENTENCE:
Evaluation of porosity in welding discloses crucial insights right into the stability and high quality of the weld joint. Porosity, defined by the presence of tooth cavities or gaps within the weld metal, is a common worry in welding procedures. These spaces, if not correctly addressed, can endanger the architectural stability and mechanical residential or commercial properties of the weld, causing possible failings in the ended up product.
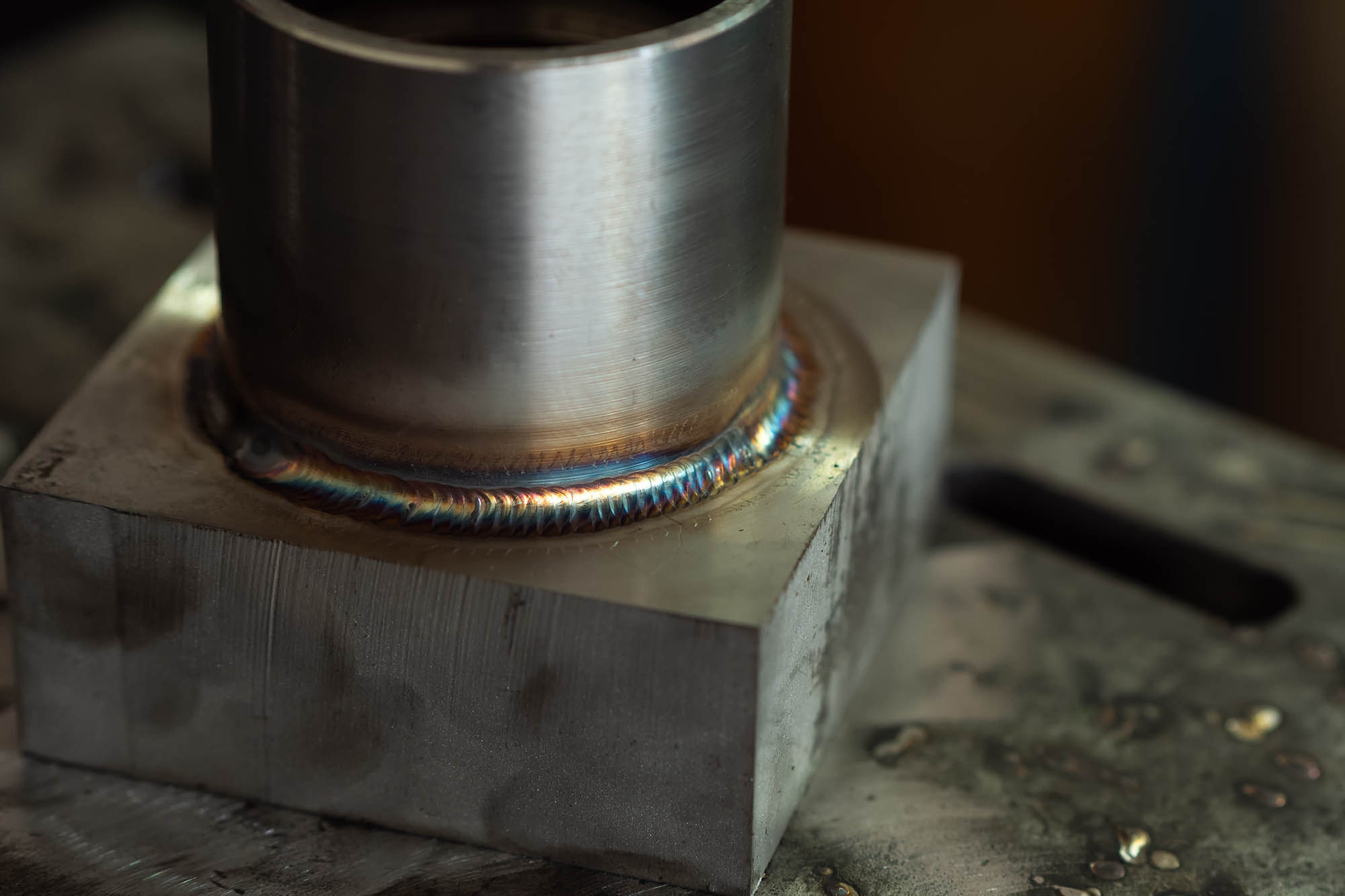
To discover and quantify porosity, non-destructive screening approaches such as ultrasonic testing or X-ray inspection are usually used. These methods enable the recognition of interior defects without endangering the stability of the weld. By analyzing the dimension, form, and distribution of porosity within a weld, welders can make enlightened choices to improve their welding procedures and achieve sounder weld joints.
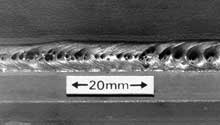
Aspects Influencing Porosity Development
The event of porosity in welding is influenced by a myriad of elements, varying from gas securing effectiveness to the ins and outs of welding criterion setups. Welding specifications, consisting of voltage, existing, travel speed, and electrode type, likewise influence porosity development. The welding method employed, such as gas metal arc welding (GMAW) or protected steel arc welding (SMAW), can affect porosity development due to variations in heat distribution and gas insurance coverage - What is Porosity.
Results of Porosity on Weld Top Quality
Porosity formation dramatically jeopardizes the structural integrity and mechanical buildings of bonded joints. When porosity exists in a weld, it creates spaces or tooth cavities within the product, minimizing the total toughness of the joint. These voids serve as tension concentration points, making the weld much more prone to splitting and failing under lots. The existence of porosity also deteriorates the weld's resistance to rust, as the trapped air or gases within deep spaces can respond with the surrounding setting, leading to degradation with time. In addition, porosity can prevent the weld's capability to endure pressure or effect, additional endangering the general high quality and dependability of the welded framework. In essential applications such as aerospace, vehicle, or structural building and constructions, where safety and security and durability are paramount, the destructive results of porosity on weld high quality can have severe effects, emphasizing the importance of visit this page reducing porosity via correct welding techniques and treatments.
Techniques to Lessen Porosity
Additionally, using the suitable welding criteria, such as the correct voltage, current, and travel speed, is important in preventing porosity. Keeping a regular arc length and angle throughout welding additionally aids reduce the likelihood of porosity.

Furthermore, picking the best shielding gas and preserving correct gas circulation prices are necessary in minimizing porosity. Making use of the appropriate welding technique, such visit the website as back-stepping or employing a weaving activity, can additionally assist disperse heat evenly and decrease the possibilities of porosity development. Finally, ensuring proper ventilation in the welding setting to get rid of any type of potential sources of contamination is crucial for accomplishing porosity-free welds. By executing these techniques, welders can properly decrease porosity and generate high-grade bonded joints.
Advanced Solutions for Porosity Control
Applying advanced technologies and innovative methods plays an essential function in achieving superior control over porosity in welding procedures. One sophisticated service is making use of innovative gas blends. Shielding gases like helium or a blend of argon and hydrogen can help in reducing porosity by giving much better arc stability and boosted gas protection. Additionally, using advanced welding techniques such as pulsed MIG welding or customized atmosphere welding can additionally assist mitigate porosity problems.
An additional advanced option entails using innovative welding tools. For instance, using tools with built-in functions like waveform control and innovative source of power can boost weld quality and decrease porosity threats. The execution of automated welding systems with precise control over specifications can significantly minimize porosity defects.
Additionally, including sophisticated tracking and assessment modern technologies such as real-time X-ray imaging or automated ultrasonic screening can aid in discovering porosity early in the welding procedure, enabling prompt corrective activities. On the whole, incorporating these advanced solutions can significantly enhance porosity control and enhance the total high quality of welded parts.
Final Thought
In conclusion, recognizing the try this site scientific research behind porosity in welding is important for welders and makers to create premium welds. By recognizing the aspects influencing porosity development and carrying out methods to lessen it, welders can enhance the general weld quality. Advanced solutions for porosity control can further boost the welding procedure and make certain a solid and reliable weld. It is necessary for welders to continually inform themselves on porosity and execute ideal techniques to accomplish ideal results.
Comments on “Comprehensive Guide: What is Porosity in Welding and Exactly How to avoid It”